Pour les demandes de stage et d'emploi, rendez-vous sur la page carrière
Process modeling in the extractive industry
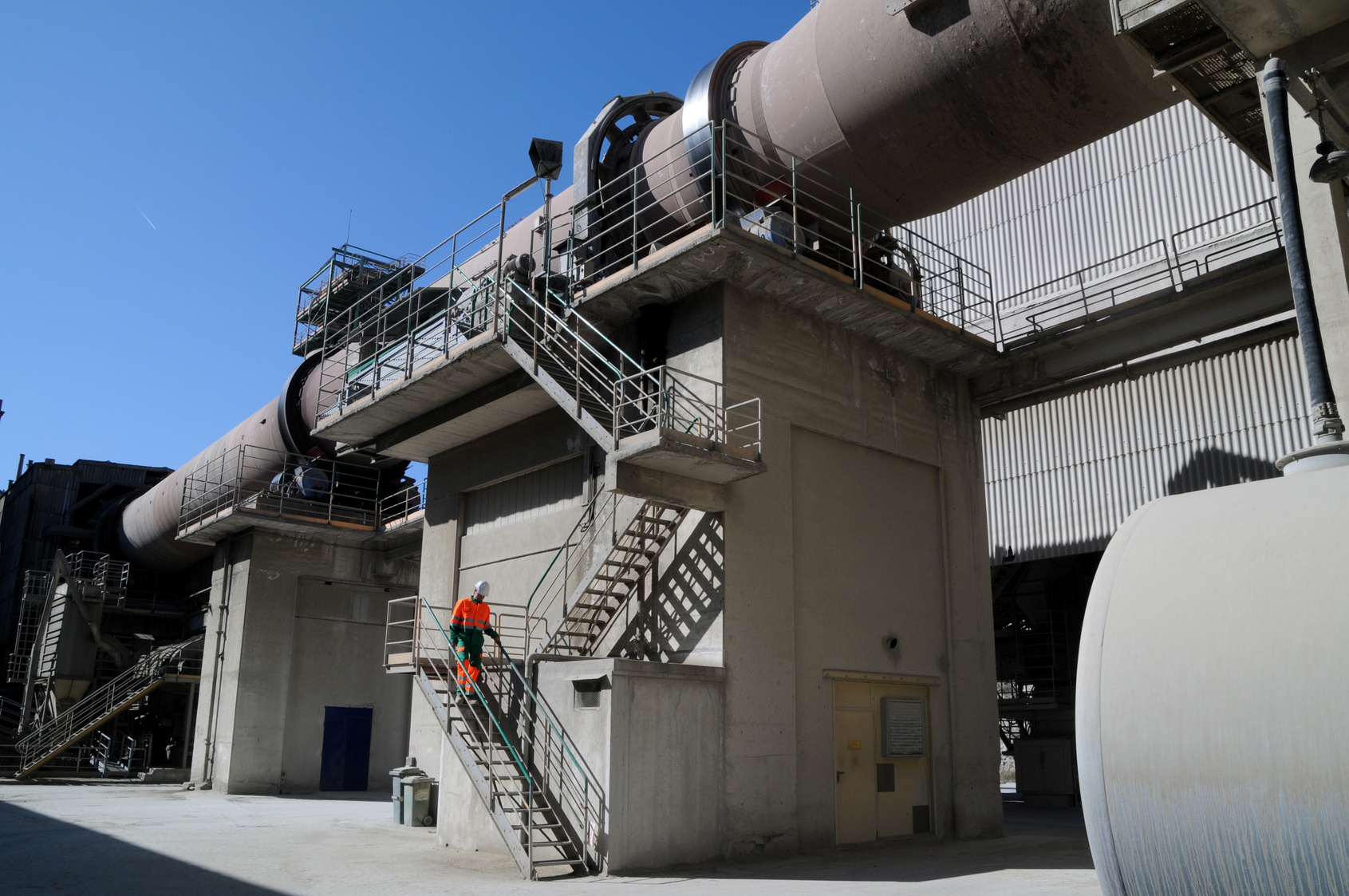
Find out how our Process Improvement team models the process to rationalize the amount of energy required and stabilize production.
Initial situation
Clinker, the basis of cement, is produced by calcining limestone around the clock. The resulting energy consumption is colossal, and therefore contributes to the process’CO2 footprint.
Raw material variability and successive chemical reactions (endothermic and exothermic) can disrupt the process , leading to oscillations that result in unwelcome consumption peaks that are difficult to control.
What’s more, these oscillations can cause technical problems, leading to impromptu furnace shutdowns and equally high restart consumption.
Solution proposed by our teams
Technord combines two approaches to process modeling , implementing mass and energy balances, backed up by data-driven Machine Learning algorithms.
Hybrid modeling and the use of historical data enable us to develop a decision-support tool for the operator.
This tool suggests energy settings to the operator, so as to stay in the ideal operating mode.
Gain for the customer
After a period of validation of the tool by process experts, the customer will obtain a “real-time” tool that instantly exploits the available measurements, corrects them if necessary, andhelps himto respect ideal production conditions.