Why integrate a DCS for industrial automation?

In today’s industrial landscape, demands for flexibility and efficiency are constantly increasing. Distributed control systems (DCS) have revolutionized manufacturing process management, enabling automated control of a large number of components, equipment and field devices that may be distributed over several industrial sites.
These so-called advanced control solutions are essential tools for manufacturers, enabling them to improve productivity and manage their operations more efficiently.
Technord, an industrial integrator from electricity to Industry 4.0 technologies, is developing solid expertise in process automation, and in particular in the implementation of high-performance DCS systems.
Let’s find out together what a DCS can do for your industry, and how Technord can transform your plant and its processes!
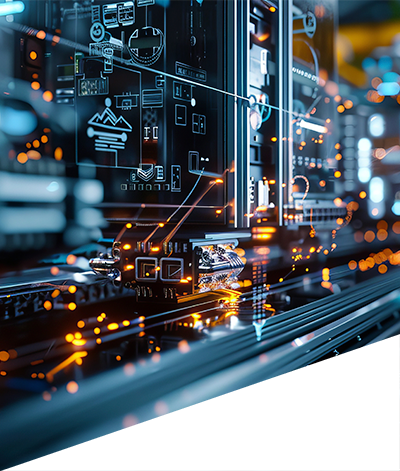
How does a distributed control system (DCS) work ?
A DCS (distributed control system) or DCS (digital control system) is an integrated platform dedicated to the automation and operation of industrial processes, based on the following points:
blank
A distributed, modular architecture
What makes DCS so special is its ability to distribute control tasks across several autonomous units, rather than relying on a single central controller.
This distributed architecture enhances the system’s resilience: if one part of the DCS encounters a problem, the other units can continue to operate, thus ensuring continuity of operations. What’s more, although DCS shares certain similarities with SCADA systems, its main focus is on process management, making it particularly well-suited to the complex needs of modern industrial environments.
Integration of sensors and actuators
The DCS interacts directly with a wide range of sensors and actuators distributed throughout the industrial plant. Sensors collect real-time data on process parameters such as temperature, pressure and flow. The actuators, in turn, execute the commands issued to adjust these parameters accordingly.
Real-time processing and control
The data collected is processed instantly by the control units. Sophisticated algorithms analyze this information and generate appropriate commands to keep processes within optimum limits. This real-time processing capability is essential to guarantee the stability and efficiency of industrial operations.
An advanced human-machine interface (HMI)
The system is distinguished by its human-machine interface(HMI), which gives operators a detailed view of the entire industrial process. Thanks to intuitive dashboards, real-time graphics and alert systems, operators can effectively monitor operations and make informed decisions.
Data historization and analysis
DCS collects and stores vast quantities of data, essential for long-term analysis,process optimization and predictive maintenance. This information enables industries to identify opportunities for improvement and adapt their operations accordingly.
Why integrate a DCS system into your industry ?
Integrating a distributed control system (DCS) into an industrial plant represents a crucial strategic investment. The motivations behind this decision are manifold, and impact on various aspects of modern production.
Adopting an up-to-date control system overcomes the challenges associated with aging technology. Obsolete systems often lack technical support and spare parts, which can compromise their efficiency. What’s more, these older technologies are unable to integrate current innovations, such as the Internet of Industrial Things (IIoT), limiting their ability to process data. As a result, it becomes difficult to operate modern equipment, which can lead to a drop in productivity. Obsolete systems are also more vulnerable to cyber attacks.
The International Trade Administration (ITA) has noted a growing demand for industrial automation, marking the advent of intelligent industry. Companies are striving to improve their product and service offerings by investing in modern equipment. In this context, the use of a captive system to integrate these innovations is essential.
Safety is a priority in all industrial sectors. A digital control system constantly monitors critical parameters, enabling rapid detection of anomalies. In the event of a dangerous situation, the system automatically activates emergency procedures, minimizing the risk of accidents. What’s more, all actions and events are logged, facilitating post-incident analysis and continuous improvement of safety protocols.
Integrating a DCS helps to improve operational efficiency. Thanks to predictive maintenance and integrated redundancy systems, downtime is reduced. What’s more, effective process control enables optimum management of raw materials and energy, thus reducing waste. More precise control also translates into more consistent, superior product quality.
In the age ofIndustry 4.0, decision-making is based on hard data.
The control system plays a central role here, with integrated analysis tools thatextract valuableinsights . This provides operators and managers with detailed, real-time information, enabling them to make informed decisions.
The advantages of the
distributed control system .
Optimal management of complex processes
In sectors such as petrochemicals, pharmaceuticals or power generation, processes are often complex, involving many interdependent variables. DCS excels in managing these systems, offering :
Precise control
The DCS allows rigorous control of every aspect of the process, guaranteeing consistent quality of the final product.
Reactivity
Thanks to its distributed architecture, the system responds quickly to variations, maintaining stable operations.
Real-time optimization
The DCS system continuously adjusts parameters to maximize production, reducing costs and improving efficiency.
Robust, reliable automation
Reliability is critical in any industrial environment. With DCS,automation is designed to isolate problems and avoid the propagation of a localized failure to the entire process.
What’s more, modern architectures incorporate advanced self-diagnosis functions, enablingearly detection of potential problems and limiting human intervention, so that operators can concentrate on value-added tasks.
Advanced alert management
DCS prioritizes alerts according to their criticality, avoiding information overload for operators. The system can also identify alert trends, helping to prevent recurring problems. These can be customized for different roles, ensuring that each user receives the information most relevant to their responsibilities.
Complete process integration
The system coordinates the interdependencies between the various processes, optimizing the entire production chain and enabling global rather than local improvement.
Upgradeable automation
Industrial automation systems need to keep pace with technological change. DCS offers remarkable flexibility, enabling new modules to be added or modified without disrupting the whole system. Modern DCSs integrate easily with other systems and technologies, facilitating the adoption of new innovations. They can also evolve with the company, adapting to increased production capacity or the addition of new product lines.
Support for continuous improvement
Integrated tools enable detailed performance analysis, making it easier to identify opportunities for improvement. Some DCSs include simulation capabilities, enabling process changes to be tested and optimized before they are actually implemented. The most advanced systems also include machine learning capabilities, enabling continuous optimization based on operational experience.
Technord, your expert in industrial automation and DCS systems integration .
Industrial automation is a complex field where the choice of an experienced partner for the integration and maintenance of distributed control systems (DCS) is essential.
Technord is a leader in this sector, offering in-depth expertise and tailor-made solutions for industries in France, Belgium and beyond. With extensive experience in a wide range of industrial sectors, we are active in the following areas:
Pharmaceuticals
Water treatment
Food industry
Chemicals and petrochemicals
Power generation
This diversity of experience enables us to offer innovative solutions, inspired by the best practices in each sector.
Comprehensive services
Technord offers a complete range of DCS-related services:
- Architecture definition: Design of an architecture adapted to the specific needs of your installation.
- Design of standard objects and libraries: Creation of customized components to optimize system performance.
- Application development: Development of customized applications to ensure efficient operations.
- Manufacturing process simulation: simulations for factory acceptance testing (FAT).
- Training: comprehensive training programs for operators and maintenance personnel
- Support and maintenance: ongoing support and preventive maintenance to ensure system longevity and efficiency.