Pourquoi intégrer un DCS pour l’automatisation industrielle ?

Dans le paysage industriel actuel, les exigences en matière de flexibilité et d’efficacité sont en constante augmentation. Les systèmes de contrôle distribués (DCS) ont révolutionné la gestion des processus de fabrication, permet d’assurer un contrôle automatisé d’un large nombre de composants, équipements et appareils de terrain pouvant être répartis sur plusieurs sites industriels.
Ces solutions dites de contrôle-commande avancées se présentent comme des outils essentiels pour les fabricants, leur permettant d’améliorer leur productivité et de gérer leurs opérations de manière plus efficace.
Technord, intégrateur industriel de l’électricité aux technologies de l’industrie 4.0, développe une solide expertise en matière d’automatisation des procédés et notamment dans la mise en œuvre de systèmes DCS performants.
Découvrons ensemble tout ce qu’un DCS peut offrir à votre industrie et comment Technord peut transformer votre usine et ses process !
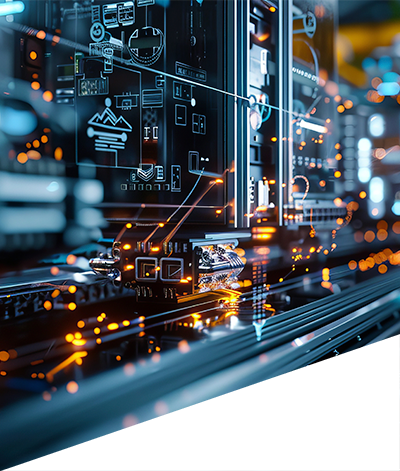
Comment fonctionne un système de contrôle distribué (DCS) ?
Un DCS (distributed control system) ou SNCC (système numérique de contrôle-commande) est une plateforme intégrée dédiée à l’automatisation et à l’exploitation des processus industriels et reposant sur les points suivants :
blank
Une architecture distribuée et modulaire
Ce qui fait la particularité du DCS, c’est sa capacité à répartir les tâches de contrôle sur plusieurs unités autonomes, plutôt que de s’appuyer sur un contrôleur central unique.
Cette architecture distribuée renforce la résilience du système : si une partie du DCS rencontre un problème, les autres unités peuvent continuer à fonctionner, assurant ainsi la continuité des opérations. En outre, bien que le DCS partage certaines similitudes avec les systèmes SCADA, il se concentre principalement sur la gestion des processus, ce qui en fait un outil particulièrement adapté pour répondre aux besoins complexes des environnements industriels modernes.
L’intégration de capteurs et actionneurs
Le DCS interagit directement avec un large éventail de capteurs et d’actionneurs répartis dans l’installation industrielle. Les capteurs collectent en temps réel des données relatives à divers paramètres du processus, tels que la température, la pression et ou encore le débit. Les actionneurs, quant à eux, exécutent les commandes émises pour ajuster ces paramètres en conséquence.
Un traitement et un contrôle en temps réel
Les données collectées sont traitées instantanément par les unités de contrôle. Des algorithmes sophistiqués analysent ces informations et génèrent des commandes appropriées pour maintenir les processus dans les limites optimales. Cette capacité de traitement en temps réel est essentielle pour garantir la stabilité et l’efficacité des opérations industrielles.
Une interface homme-machine (IHM) avancée
Le système se distingue par son interface homme-machine (IHM), qui offre aux opérateurs une vue détaillée de l’ensemble du processus industriel. Grâce à des tableaux de bord intuitifs, des graphiques en temps réel et des systèmes d’alerte, les opérateurs peuvent surveiller efficacement les opérations et prendre des décisions éclairées.
Une historisation et analyse des données
Le DCS collecte et stocke de vastes quantités de données, essentielles pour l’analyse à long terme, l’optimisation des processus et la maintenance prédictive. Ces informations permettent aux industries d’identifier les opportunités d’amélioration et d’adapter leurs opérations en conséquence.
Pourquoi intégrer un système DCS dans votre industrie ?
L’intégration d’un système de contrôle distribué (DCS) dans une installation industrielle représente un investissement stratégique crucial. Les motivations derrière cette décision sont multiples et impactent divers aspects de la production moderne.
L’adoption d’un système de contrôle-commande à jour permet de surmonter les défis associés à une technologie vieillissante. En effet, les systèmes obsolètes présentent souvent un manque de support technique et de pièces de rechange, ce qui peut compromettre leur efficacité. De plus, ces anciennes technologies ne peuvent pas intégrer les innovations actuelles, telles que l’Internet des objets industriels (IIoT), limitant ainsi leur capacité à traiter les données. En conséquence, l’exploitation d’équipements modernes devient difficile, ce qui peut entraîner une baisse de la productivité. Par ailleurs, les systèmes obsolètes sont également plus vulnérables aux cyberattaques.
L‘Administration du commerce international (ITA) constate une demande croissante pour l’automatisation industrielle, marquant ainsi l’avènement de l’industrie intelligente. Les entreprises s’efforcent d’améliorer leur offre de produits et de services en investissant dans des équipements modernes. Dans ce contexte, l’utilisation d’un système capé pour intégrer ces innovations est essentiel.
La sécurité constitue une priorité dans tous les secteurs industriels. Un système numérique de contrôle-commande surveille en permanence les paramètres critiques, permettant une détection rapide des anomalies. En cas de situation dangereuse, le système active automatiquement des procédures d’urgence, minimisant ainsi les risques d’accidents. De plus, toutes les actions et événements sont enregistrés, facilitant l’analyse post-incident et l’amélioration continue des protocoles de sécurité.
L’intégration d’un DCS contribue à améliorer l’efficacité opérationnelle. Grâce à la maintenance prédictive et à des systèmes de redondance intégrés, les temps d’arrêt sont réduits. De plus, un contrôle efficace des processus permet une gestion optimale des matières premières et de l’énergie, diminuant ainsi le gaspillage. Un contrôle plus précis se traduit également par une qualité de produit plus constante et supérieure.
À l’ère de l’industrie 4.0, la prise de décision s’appuie sur des données concrètes. Le système de contrôle joue un rôle central dans ce cadre, avec des outils d’analyse intégrés qui permettent d’extraire des insights précieux. Les opérateurs et les gestionnaires disposent ainsi d’informations détaillées et en temps réel, leur permettant de prendre des décisions éclairées.
Les atouts du système
de contrôle distribué .
Gestion optimale des processus complexes
Dans des secteurs tels que la pétrochimie, la pharmacie ou la production d’énergie, les processus sont souvent complexes et impliquent de nombreuses variables interdépendantes. Le DCS excelle dans la gestion de ces systèmes en offrant :
Contrôle précis
Le DCS permet un contrôle rigoureux de chaque aspect du processus, garantissant une qualité constante du produit final.
Réactivité
Grâce à son architecture distribuée, le système répond rapidement aux variations, maintenant ainsi la stabilité des opérations.
Optimisation en temps réel
Le système DCS ajuste en continu les paramètres pour maximiser la production, réduisant ainsi les coûts et améliorant l’efficacité.
Une automatisation robuste et fiable
La fiabilité est un aspect critique dans tout environnement industriel. Grâce au DCS, l’automatisation est conçue pour isoler les problèmes et éviter la propagation d’une défaillance localisée à l’ensemble du processus.
De plus, les architectures modernes intègrent des fonctionnalités d’auto-diagnostic avancées, permettant une détection précoce des problèmes potentiels qui limite l’intervention humaine, pour mieux concentrer les opérateurs sur les tâches à valeur ajoutée.
Gestion avancée des alertes
Le DCS priorise les alertes en fonction de leur criticité, évitant ainsi une surcharge d’informations pour les opérateurs. Le système peut également identifier les tendances des alertes, aidant à prévenir les problèmes récurrents. Ces dernières sont personnalisables en fonction des différents rôles, garantissant que chaque utilisateur reçoit les informations les plus pertinentes pour ses responsabilités.
Intégration complète des processus
Le système coordonne les interdépendances entre les différents processus, optimisant ainsi toute la chaîne de production, permettant une amélioration globale plutôt que locale.
Automatisme évolutif
Les systèmes d’automatisation industrielle doivent s’adapter à l’évolution technologique. Le DCS offre une flexibilité remarquable, permettant l’ajout ou la modification de nouveaux modules sans perturber l’ensemble du système. Les DCS modernes s’intègrent facilement avec d’autres systèmes et technologies, facilitant l’adoption de nouvelles innovations. Ils peuvent également évoluer avec l’entreprise, s’adaptant à l’augmentation de la capacité de production ou à l’ajout de nouvelles lignes de produits.
Support de l’amélioration continue
Les outils intégrés permettent une analyse détaillée des performances, facilitant l’identification des opportunités d’amélioration. Certains DCS incluent des capacités de simulation, permettant de tester et d’optimiser les changements de processus avant leur mise en œuvre réelle. Les systèmes les plus avancés comprennent également des fonctionnalités d’apprentissage automatique, favorisant ainsi une optimisation continue basée sur l’expérience opérationnelle.
Technord, votre expert en automatisation industrielle et intégration de systèmes DCS .
L’automatisation industrielle est un domaine complexe où le choix d’un partenaire expérimenté pour l’intégration et la maintenance de systèmes de contrôle distribués (DCS) est essentiel.
Technord se positionne comme un leader dans ce secteur, offrant une expertise approfondie et des solutions sur mesure adaptées aux industries en France, en Belgique et au-delà. Avec une vaste expérience dans divers secteurs industriels, nous intervenons dans les domaines suivants :
Pharmaceutique
Traitement des eaux
Agroalimentaire
Chimie et pétrochimie
Production d'énergie
Cette diversité d’expérience nous permet de proposer des solutions innovantes, inspirées des meilleures pratiques de chaque secteur.
Des services complets
Technord offre une gamme complète de services liés aux DCS :
- Définition de l’architecture : Élaboration d’une architecture adaptée aux besoins spécifiques de votre installation.
- Conception d’objets et de bibliothèques standards : Création de composants sur mesure pour optimiser les performances du système.
- Développement d’applications : Développement d’applications personnalisées pour garantir l’efficacité des opérations.
- Simulation des procédés de fabrication : Réalisation de simulations pour effectuer les tests d’acceptation en usine (FAT).
- Formation : programmes de formation complets pour les opérateurs et le personnel de maintenance
- Support et maintenance : service de support continu et maintenance préventive pour assurer la longévité et l’efficacité du système.